DEEP INSPECTION
Automated inspection of railway infrastructure
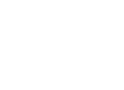
Over 100,000 km of railway analyzed
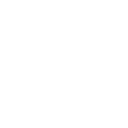
Works with any camera system
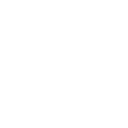
Run on-board or in the cloud
Best-in-class machine learning algorithms for…
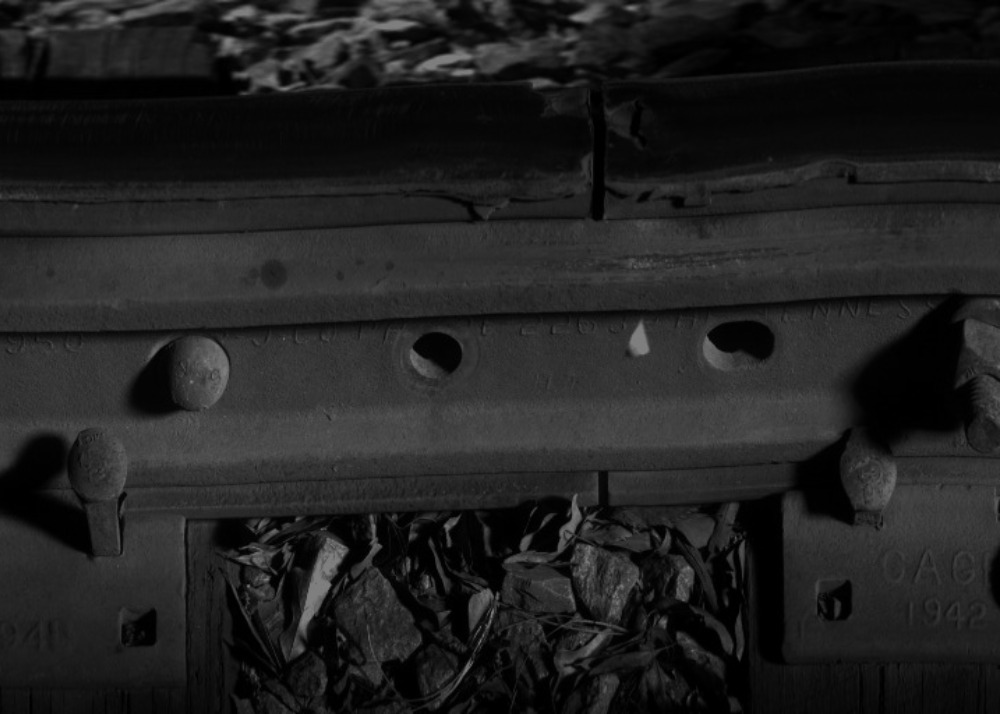
Track Inspection
We search for damage such as sleeper cracks, damaged fastenings, squats, shelling, and head-checks.
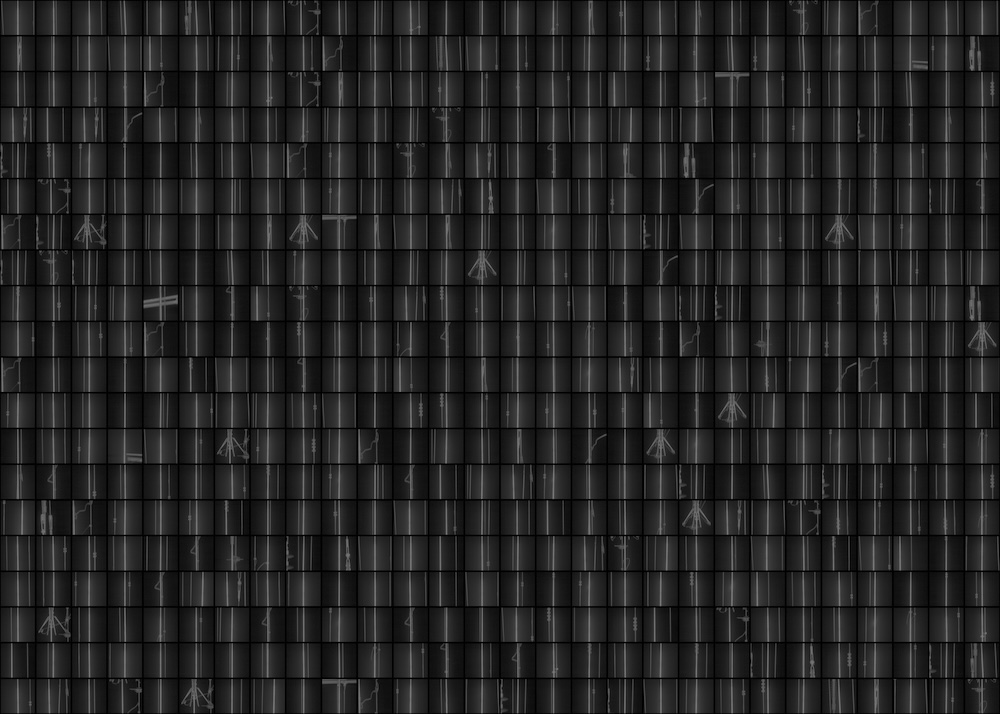
Catenary Inspection
Above the train, we monitor the catenary system and detect defects such as broken strands and catenary splices.
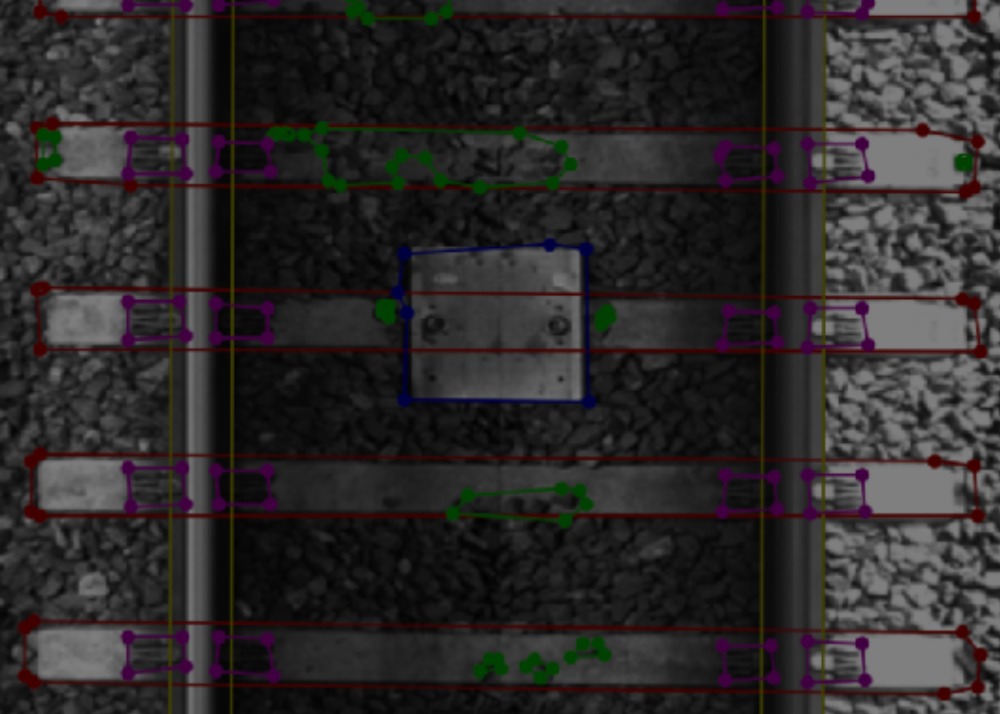
Digital Inventory
Know the exact position and condition of every essential component in your railway network
Track Inspection
Our algorithms detect damage such as sleeper cracks, damaged fastenings, squats, and head-checks in everything from line cameras to drone imagery.
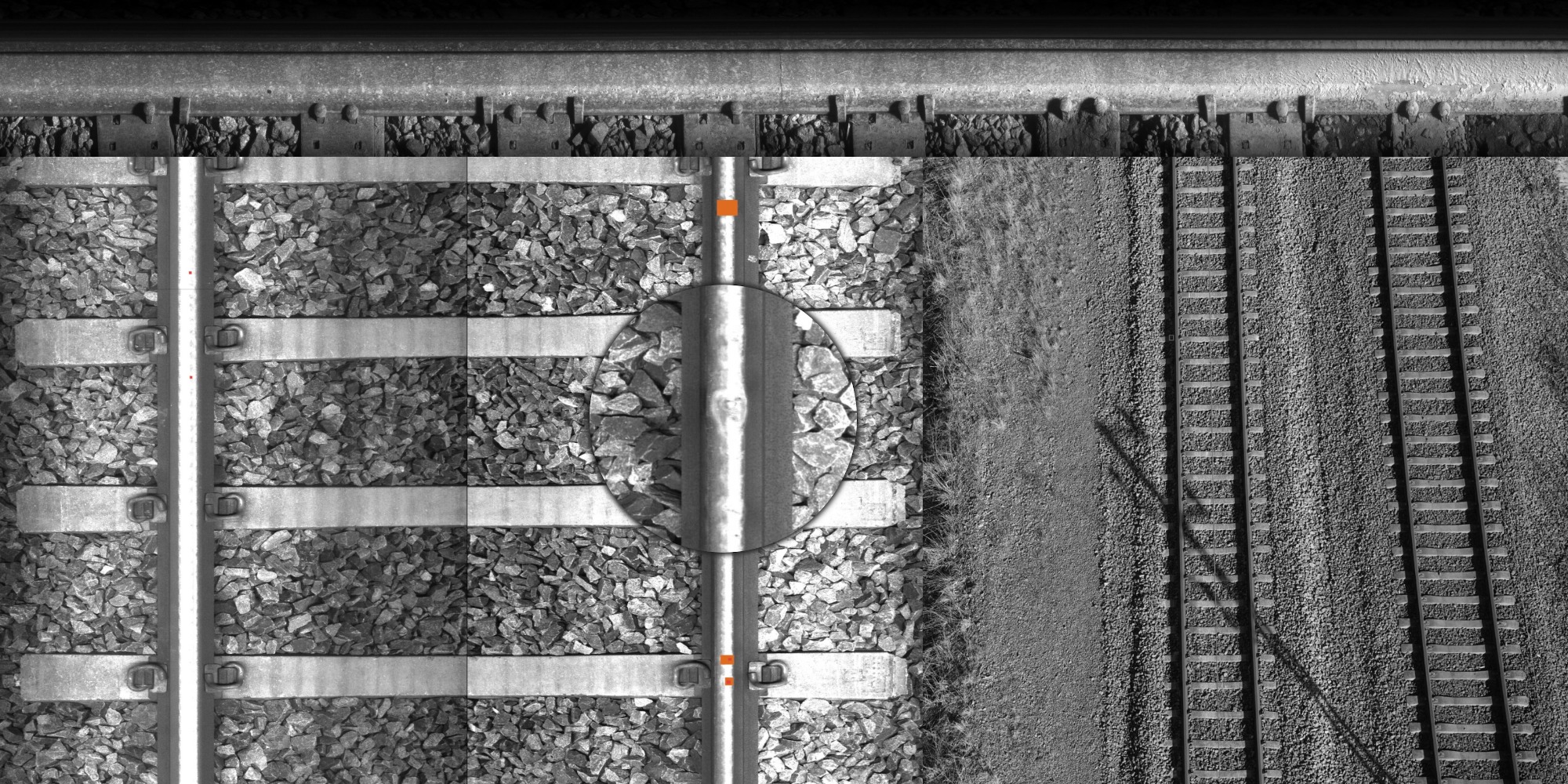
Detecting cracks in sleepers
Instead of saying that a crack exists, the algorithm masks the damage, which allows us to measure its length, width, and whether it reaches the fastening.
Missing and damaged fastenings
Our algorithm detects if a fastener is missing or if it’s damaged. We only need a few examples to inspect a new type of fastening automatically.
rail-head damage and anomalies
On the railheads, our algorithms analyze images from the side or from above to detect damage such as cracks, spalling, squats, shelling, and head-checks.
Welds and rail joints
In addition to common damage, we locate and assess components such as welds and rail joints that may exhibit a range of severe anomalies.
Catenary Inspection
Our catenary inspection algorithms have analyzed over 2 billion examples in the Nordics, and can process images at speeds of 180 km/h.
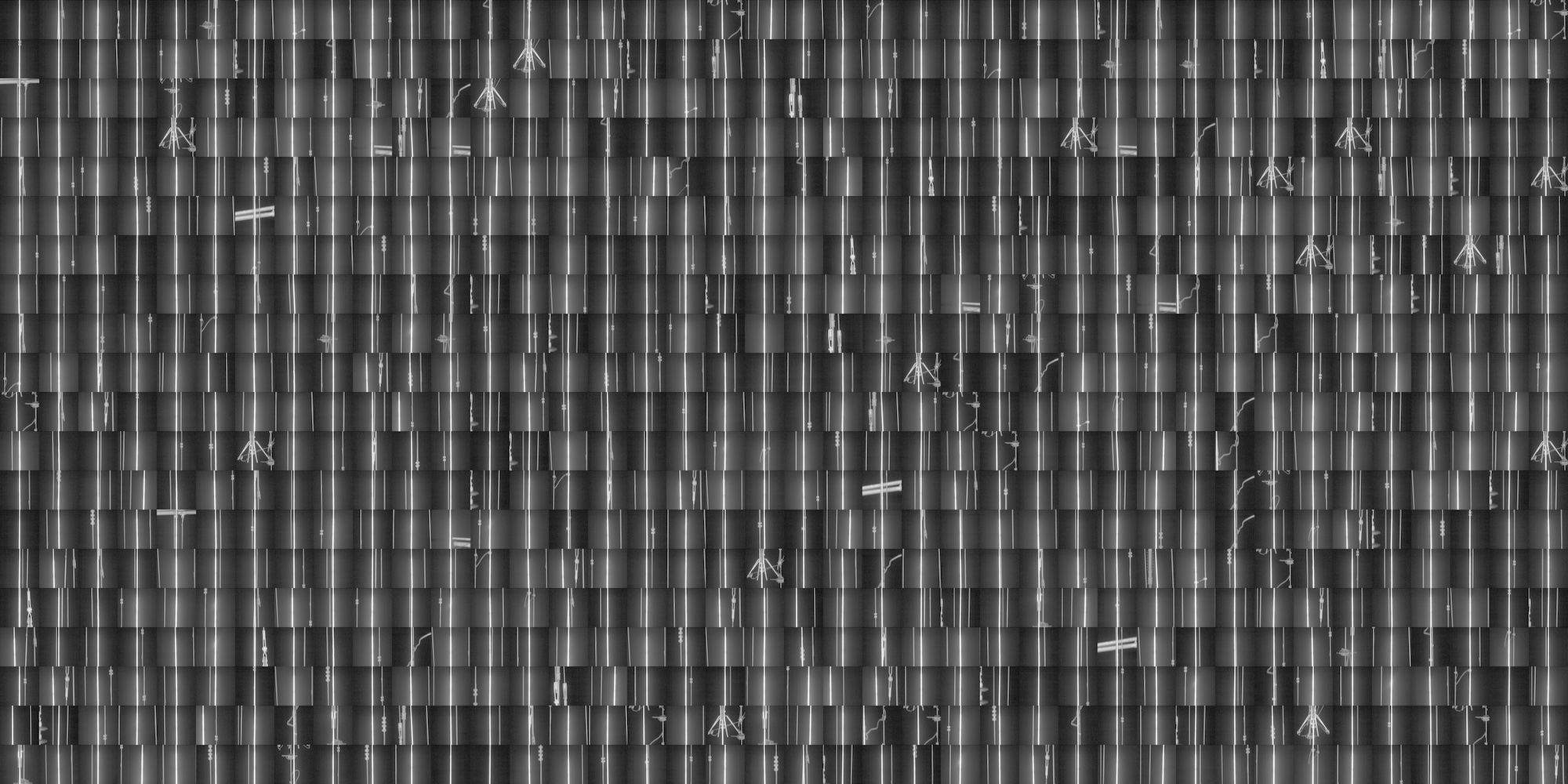
Broken strands and other anomalies
Above the train, Deep Inspection monitors the catenary system to detect anomalies such as broken strands and catenary splices.
We only have a single confirmed false negative and around 10% false positives for our work in the Nordics, which is amazing considering the volume of images.
Real examples from Technicians at detected locations
As soon as there’s a connection to the internet, we send suspected damage to a user interface for additional manual inspection.
Below are a few examples where technicians have visited a location marked by the Deep Inspection algorithms.
As soon as there’s a connection to the internet, we send suspected damage to a user interface for additional manual inspection.
Below are a few examples where technicians have visited a location marked by the Deep Inspection algorithms.
Digital Inventory
Know the exact position and condition of every essential component in your railway network
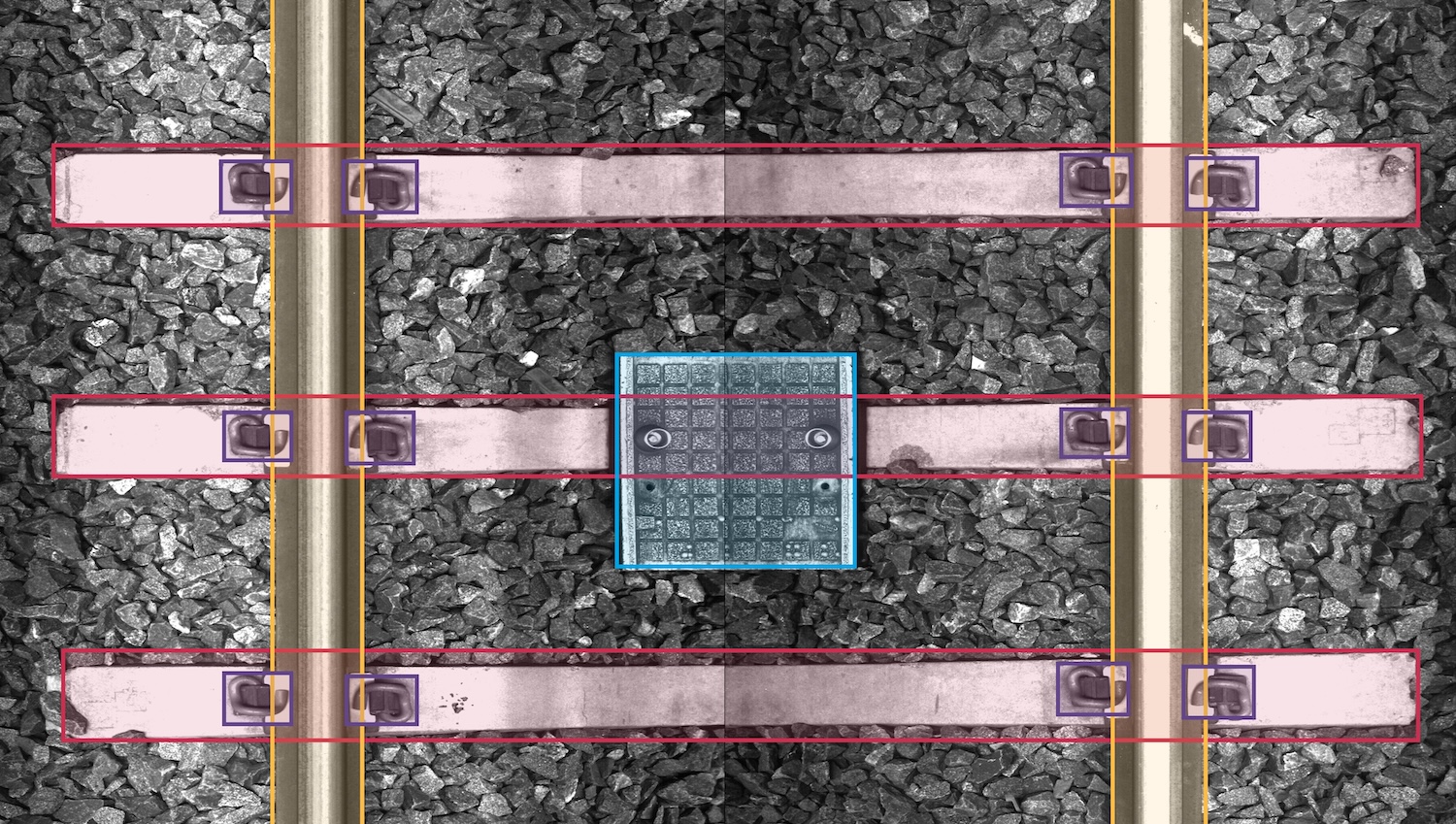
A popular feature for our current customers is the ability to know exactly what components you have in your network and where.
Most internal systems with information about components become outdated quickly and are often inaccurate.
With Deep Inspection, service technicians get access to an updated and complete digital inventory of relevant assets.
Positioning and damage over time
By using positions for detected components, we can align different measurements of the same area to measure wear and to see how damage develops over time.
Component status
In addition to specific damage detection, Deep Inspection assesses every component to measure if it looks strange in any way.
Additional Information
There are a few more things that you should know about the capabilities and features of Deep Inspection
Type of data
Deep Inspection works for any images or video of railway infrastructure as long as damage are visible to the human eye.
Currently, we analyze data from line scan cameras mounted on trains and drone imagery.
Cloud or Edge
You can run Deep Inspection directly in your measurement train, in the cloud, or at some other location with access to a GPU.
We aim to build software that’s easy to integrate with the customer’s current systems.
Integration
We adjust and export the results in a format that’s compatible with current workflows and often integrate Deep Inspection directly to other systems.
Customers can also select the modules that deliver the most values to them.
User interfaces
You can choose to include the Deep Inspection user interface for complementary manual inspection, monitoring algorithms, exporting results, and managing damage.
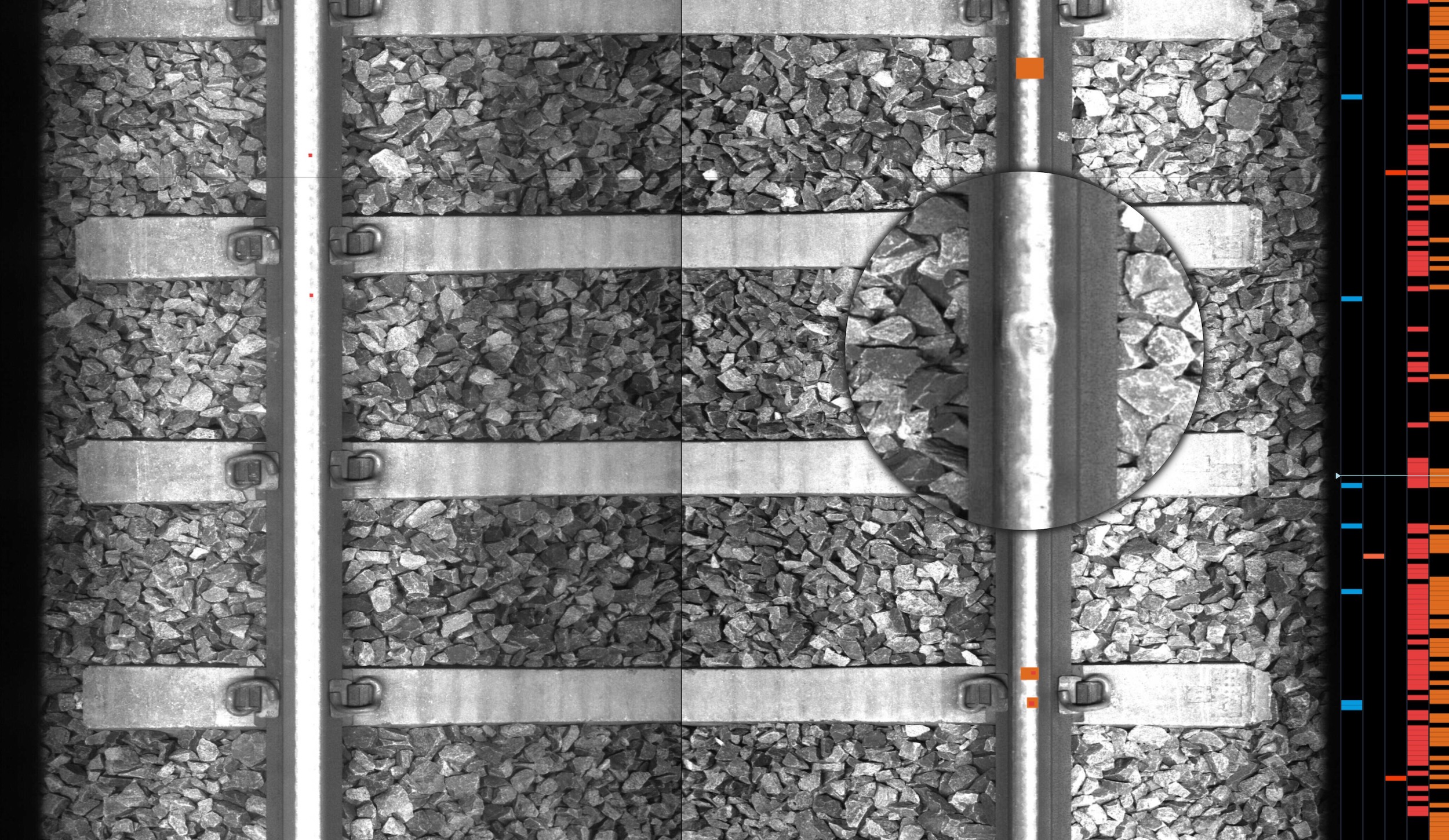
Contact Us
Oscar Johansson
CEO
+46 72 005 05 85
oscar@nextml.com
© 2023 – All Rights Reserved.